Six Sigma este? Proiect ca proces sau proces ca proiect
În 1986, Motorola a fost atât de afectată de un defect de fabricație încât inginerul său, Bill Smith, a venit cu o metodologie pentru a reduce defectele la inexactitate matematică. Așa a apărut metoda Six Sigma, pe care alți giganți industriali și financiari se vor înarma în curând.
Six Sigma este un concept din teoria probabilității, exprimat prin formula: nu mai mult de 3,4 defecte per milion de produse sau procese. Sarcina matematică a metodologiei este de a reduce dispersia opțiunilor.
Adică la propriu 6 Sigma este o metodologie de management de proiect axată pe eliminarea defectelor de fabricație ca clasă.
Principii
- Faceți procesele previzibile
- Încercați să vă asigurați că procesele de producție și de afaceri pot fi descrise, măsurate, analizate, îmbunătățite și controlate
- Pentru a reuși cu Six Sigma, implicați toți oamenii din organizație, în special conducerea de vârf.
- Stabiliți obiective specifice care pot fi calculate sau măsurate: reducerea costurilor cu 20%, creșterea profitabilității cu o treime, reducerea ciclului de producție cu o oră
- Atrageți manageri cu abilități puternice de leadership și ascultare
- Luați decizii bazate pe informații și statistici dovedite, mai degrabă decât pe presupuneri.
Algoritmi
Six Sigma oferă două abordări, în funcție de faptul că îmbunătățiți procesul - DMAIC sau creați un produs nou - DMADV, alias DFSS. Ambele metode pot fi descrise prin formula Planificați-Efectuați-Verificați-Remediați.
- Definiți obiectivele proiectului și nevoile clienților. Formați o echipă de proiect, stabiliți-i aria de responsabilitate și atribuiți autoritatea.
- Colectați date curente, „măsurați” parametrii cheie ai procesului.
- Analizați informațiile colectate și identificați factorii care afectează calitatea organizatieisau activitate de afaceri. Găsiți cauza principală a căsătoriei și defectele, sugerați metode cum să o eliminați.
- Îmbunătățiți sau optimizați procesele curente. Faceți modificări de probă.
- Monitorizați-vă editările, astfel încât orice abateri de la obiectiv să nu ducă din nou la defecte. Raportați progresul proiectului pe panouri informative, urmăriți cum funcționează acestea cu statisticile. Repetați procesul până când ajungeți la calitatea dorită.
Principiul principal al DMAIC este să fii proactiv. Trebuie prevăzute noile preferințe ale consumatorilor, trebuie prevenite defectele.
Algoritmul DMADV sau DFSS
- Definiți obiectivele care ar trebui să se alinieze cu dorințele clienților și cu strategia de afaceri. Creați o echipă de proiect.
- Indicați principalele caracteristici ale produsului, nevoile ciclului de producție.
- Găsiți și analizați mai multe opțiuni.
- Alegeți cea mai bună opțiune și începeți să lucrați la ea.
- Pune-ți proiectul în practică.
Instrumente
Pot fi utilizate atât principiile managementului calității, cât și metodele statistice. Primele sunt:
- „5 de ce”. Ne punem această întrebare până aflăm cauza principală a defectelor.
- Schițăm ce resurse avem și ce trebuie făcut. De exemplu, iată o hartă a proceselor la comandarea și expedierea mărfurilor:
- Analiza cost-beneficiu. Când există mai multe opțiuni de proiect, alegeți-o pe cea cu cel mai bun raport beneficiu-cost.
- Arborele parametrilor critici de calitate (arborele CTQ). Desenați o diagramă cu caracteristicile cheie pentru proiectul dvs. De exemplu, aici este un copac pentru crearea unui magazin de îmbrăcăminte pentru copii.
- Planificarea experimentului. Ajută la efectuarea cercetării mai eficient și la pregătirea pentru experimente.
Instrumentele statistice includ:
- ANOVA
- Analiza regresiei
- Diagramă de dispersie
- Cardul de control Shewhart
- curba Pareto.
Ierarhie
Conceptul de management amintește de artele marțiale orientale. Rolul interpretului depinde de centura sa - nivelul de cunoștințe și abilități ale Six Sigma.
- În vârful piramidei se află Conducerea principală ... Aloca responsabilități și resurse.Conducerea principalădistruge barierele interne și combate rezistența înnăscută a personalului la schimbare.
- Campioniimplementează metodologia în organizație și îndrumă proprietarii Centuri negre.
- Maeștrii centurii negresupraveghează desfășurarea Six Sigma și comandă Centurile Negre obișnuite.
- Centuri negresub supravegherea masteranților, aceștia sunt angajați într-un proiect și îndeplinesc sarcinile care le sunt atribuite;
- Centuri verzi- este vorba de personal care, pe lângă atribuțiile lor, lucrează la implementarea metodologiei. Urmareste asta Centuri negre.
- Uneori izolat Centuri Albeși Centuri galbene - angajați ai companiei care cunosc Six Sigma la nivelul inițial și fie participă parțial la proiect, fie urmăresc acțiunile colegilor cu experiență.
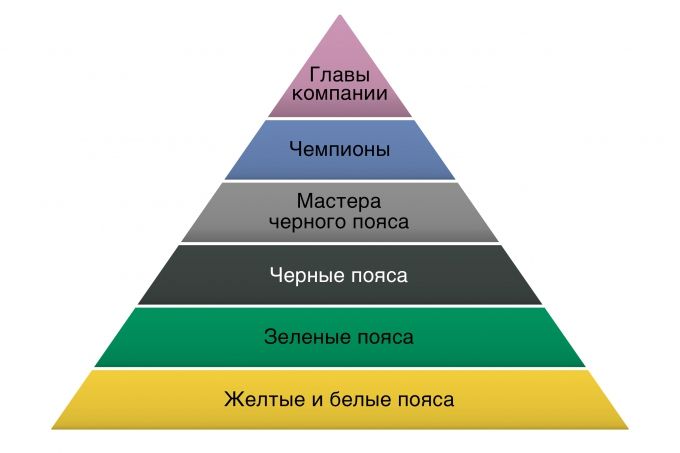
Puteți obține certificarea în companii și. Instruirea are loc atât la fața locului, în Statele Unite, cât și online. De asemenea, puteți susține examene de pe computer, instalând un software special.
Certificatele sunt emise și de către dezvoltatorul metodologiei, compania. Cursurile de formare sunt organizate nu numai în America de Nord, ci și în Europa, Asia, Africa.
Diferențele față de metodologii similare
De la sfârşitul anilor 2000. Metodologia a devenit populară - o combinație de abordări Lean, lean manufacturing și Six Sigma. Misiunea Lean este de a reduce costurile și de a spune la revedere fluxurilor de lucru care nu oferă valoare consumatorului. De asemenea, ajută la standardizarea producției.
Metodologia Six Sigma are ca scop reducerea defectelor și necesită un control sporit al procesului. Six Sigma, cu analiza sa statistică, este aproape o disciplină tehnică în comparație cu Lean, unde controlul vizual este mai implicat și organizarea locului de muncă este reorganizată.
Six Sigma și Lean sunt comparate cu o altă metodologie (pentru mulți este mai mult o filozofie corporativă) -. De asemenea, necesită ca organizația să îmbunătățească și să standardizeze continuu procesele. Cu toate acestea, principala diferență a Kaizen este accentul pus pe soluții rapide și simple, care sunt discutate deschis cu personalul.
dezavantaje
- Tot mai multe organizații au început să pregătească viitorii deținători de Centura Neagră ... Drept urmare, spun criticii, calitatea certificării a scăzut. Centuri negre sunt eliberate cu mai puține cunoștințe.
- Revista Fortune a susținut că aproape toate cele 58 de companii mari care au promis loialitate Six Sigma apoi au renunțat la S&P 500. Metodologia Six Sigma,jurnaliștii publicației de afaceri insistă, nu ajută la crearea de produse și tehnologii inovatoare.
- Acest lucru se poate datora unui alt dezavantaj că Six Sigma este creditat cu limitarea libertății creative. Potrivit acestei opinii, „măsurătorile” constante și analiza statistică nu permit echipei de proiect să se angajeze în brainstorming și să vină cu o idee neașteptată. Metodologia are un algoritm riguros și urmărește în primul rând scopuri comerciale, nu inovatoare.
- Ascunderea lui Six Sigma în statistici a fost, de asemenea, subiect de critici. Controverse teoretice fac furie în jurul unor instrumente care ar putea să nu ia în considerare pe deplin riscurile.
Ce este Six Sigma în managementul timpului?
Repere metodologiei Six Sigma de două ori - timp de conducere și de ciclu.
- Timp de conducere vorbește despre cât a trecut de la solicitarea clientului și de la primirea produsului/serviciului.
- Durata cicluluiînseamnă numărul de ore necesare pentru a finaliza un ciclu de producție sau a lucra la un proces.
EDR este o companie americană care permite rezolvarea online a problemelor juridice legate de imobiliare, de la cumpărare/vânzare până la eliberarea de certificate. Clienții ei includ avocați, asigurători, agenții guvernamentale, agenți imobiliari și evaluatori. Compania și-a stabilit un obiectiv de a îmbunătăți timpul de livrare - să furnizeze serviciul în 24 de ore de la momentul primirii cererii. Pentru aceasta s-a folosit metodologia Lean Six Sigma și algoritmul DMAIC.
În software-ul EDR, funcționau contoare automate, care înregistrau cât timp dura un anumit proces. Calculele au arătat că timpul de conducere în companie este de 50,1 ore - de două ori mai lung decât obiectivul stabilit. Dacă proiectul are succes, EDR va economisi 1 milion de dolari pe an.
Etapa 2 - Colectarea datelor
În timpul analizei datelor, Black Belts a constatat următoarele defecte:
- Personalul nu a articulat exact ce să ia în considerare la timpul de conducere. De exemplu, dacă să includă pauzele de prânz și vacanțele.
- Clienții au trimis adesea cereri în afara orelor de lucru, care nu au fost urmărite de sistem. S-a dovedit că ghișeul nu a înregistrat unele procese pregătitoare, iar timpul de conducere în companie durează chiar mai mult de 50,1 ore.
Când managerii de proiect (PM) au stabilit parametri mai specifici pentru numărătoarea inversă, timpul de livrare a fost de 67,5 ore. Cu toate acestea, schimbarea abordării statistice nu s-a potrivit pentru acționarii și personalul EDR. Timpul de conducere anterior a influențat direct prețurile serviciilor și politica de personal. Angajații nu au vrut să accepte noua metodă de evaluare a muncii lor și au vrut să lucreze ca până acum.
Aceste dificultăți psihologice au fost rezolvate atunci când PM-urile au început să comunice regulat cu conducerea și personalul pentru a lucra împreună la idei noi.
Etapa 3 - Analiza
PM a folosit diagrama Ishikawa, modul de defecțiune și analiza efectului și metoda Six Sigma „5 Why” pentru a evidenția posibilele defecte:
- Prea multe întârzieri între fluxurile de lucru
- Unele procese durează prea mult, crescând în general timpul de livrare.
- Solicitările clienților sunt primite în afara programului de lucru și pot fi procesate mai târziu de la începutul zilei următoare.
- O aplicație necesită mai multe procese diferite, ceea ce crește timpul de livrare în această situație
- Informațiile din baza de date vin în diferite formate de fișiere, iar unele dintre ele sunt dificil de procesat
- Solicitările individuale nu se încadrează în protocolul standard și necesită intervenția personală a departamentului IT
- Angajații „împrăștie” cererile primite și nu le rezolvă imediat.
4 și 5 etape - Îmbunătățire și control
PM a verificat fiecare dintre posibilele defecte și a concluzionat că intervalele lungi dintre procesele de lucru au fost problema cheie. Mai mult, timpul dintre operații a depășit timpul necesar pentru a lucra.
Prin urmare, PM-urile au redistribuit responsabilitățile astfel încât un angajat să poată efectua acum mai multe procese și să nu aștepte ca colegul său să-și facă față sarcinii sale. Această măsură a îmbunătățit flexibilitatea organizațională și a ușurat monotonia fluxului de lucru.
PM a prezentat proiectul pilot conducerii și personalului. După comentariile și dorințele angajaților, planul a fost modificat. Artiștii au urmat un antrenament suplimentar înainte ca contoarele să fie reactivate. Proiectul s-a dovedit a fi de succes: timpul de conducere a durat acum 23 de ore.
Ce este Six Sigma în industrie
Asahi India este filiala indiană a companiei japoneze Asahi. Filiala produce sticlă pentru mașini. Unul dintre modele, geamul hayonului ME3, a fost produs cu o deșeuri medie de 86,8%. Consiliul și-a stabilit un obiectiv de a reduce probabilitatea apariției defectelor, iar echipa de management al proiectului (PM) a trecut la treabă.
Metodologia six sigma, și anume algoritmul DMAIC, trebuia să salveze situația. Procesul de producție s-a desfășurat în 3 etape:
- Etapa pregătitoare ... Sticla a primit forma dorită, după care marginile au fost lustruite, spălate, uscate și inspectate.
- Sigiliu ... Pe suprafața de sticlă a fost aplicată cerneală specială, care a fost apoi uscată în compartimentele cuptorului. Acest strat protejează de razele soarelui.
- Întărire și prelucrare ... Sticla este încălzită la temperatura dorită, îndoită la o formă predeterminată și răcită cu un curent de aer de înaltă presiune. După care se examinează și se trimite spre vânzare.
Etapa 1 - Cunoașterea proiectului
Defectul de fabricație a început odată cu achiziționarea unui cuptor universal, asupra căruia a insistat firma-mamă. Noul echipament trebuia să facă sticlă atât pentru ușile laterale, cât și pentru cele din spate ale mașinii. Cu toate acestea, geamurile din spate s-au dovedit a fi mult mai defecte decât se aștepta și nu au fost întotdeauna mulțumite de calitatea consumatorilor.
Trei etape ale procesului de producție au ieșit cu următorul procent de defecte:
Etapa pregătitoare - 1,5%
Imprimare - 1,5%
Întărire și prelucrare - 10,5%.
Conducerea companiei se aștepta ca aceste cifre să fie de 0,5% pentru primele două etape și de 6,5% pentru ultima.
Echipa de proiect a realizat o diagramă în care producția a fost descompusă în procese mici și a identificat următoarele defecte:
Proces |
Defect |
Descriere |
|
pregătitoare |
Rupt |
Pesmetul se desprinde de pe margini |
|
Marginile sunt tăiate în contact cu discul de șlefuit |
|||
Gresit |
Parțial fără cerneală la suprafață |
||
Dusty Mark |
Particulele de praf lovesc suprafața imprimată |
||
Întărirea și tratament |
Imprimare bobine de cuptor |
Particulele străine rămân pe sticlă |
|
Distrugerea din fluxul de aer |
Sticla s-a spart în fragmente mici în timpul răcirii cu aer de înaltă presiune |
||
Îndoire greșită |
Sticla nu este îndoită la forma dorită |
Etapa 2 - Colectarea datelor
PM-urile au compilat o matrice cauză și efect pentru a identifica relațiile dintre procesele de producție și producție. Se acordă 3 note: 1 - corelație slabă, 3 - corelație medie și 9 - corelație ridicată.
S-a dovedit că în timpul întăririi și prelucrării, cea mai problematică etapă, defectele pot fi asociate cu temperatura din fiecare dintre cele 4 compartimente ale cuptorului, temperatura sticlei și viteza cuptorului.
Etapa 3 - Analiza
PM a văzut aproape o mie de matrițe de sticlă într-o zi, inspectându-le la fiecare jumătate de oră în timpul producției. S-au făcut măsurători detaliate pentru fiecare parametru de producție. Analiza statistică a identificat cauzele fundamentale ale defectelor.
După cum avertizează Matricea Cauză și Efect, în timpul întăririi și procesării, au apărut rebuturi din cauza abaterilor temperaturii cuptorului și sticlei, precum și din cauza vitezei liniei de producție.
În etapa pregătitoare, au apărut defecte din cauza presiunii excesive asupra materialului, a fixării necorespunzătoare și a forței excesive a echipamentului de tăiere. În timpul tipăririi, problemele au fost cauzate de filmul umed, temperaturi prea uscate, încărcarea plăcii de încărcare înapoi în mașină și distanțierele de sticlă insuficiente.
Etapa 4 - Îmbunătățire
PM a condus planificarea experimentelor. A fost selectat un complex special pentru fiecare etapă a procesului de producție.
Pentru etapa pregătitoare au fost pregătite 16 soluții noi. PM a experimentat cu setările echipamentului de tăiere și parametrii de fixare. Ca urmare, rata defectelor a scăzut la 0,5%.
În timpul fazei de tipărire, echipa de proiectare a experimentat grosimea și temperatura distanțierului. Drept urmare, procentul de defecte a fost redus și el la 0,5%.
În timpul întăririi și procesării PM, au fost efectuate 400 de iterații pentru fiecare dintre cele 16 variante pentru a obține performanțe îmbunătățite. Echipa a calculat temperatura optimă pentru fiecare dintre compartimentele cuptorului și viteza corectă pentru linia de producție.
Acum rata de respingere a scăzut la 3%, ceea ce s-a dovedit a fi chiar mai bună decât ținta stabilită de 6,5%.
Etapa 5 - Control
Scăderea deficienței trebuia încă consolidată. PM a întocmit un plan de control, care a indicat parametrii necesari pentru cuptor și linia de producție. Ei au distribuit, de asemenea, cine va monitoriza procesele, cât de des să facă acest lucru și ce dispozitive de măsurare să folosească pentru aceasta.
Aplicare de către marile companii
Metodologia Six Sigma a fost dezvoltată în companie Motorola... Conducerea ei a fost nemulțumită că 5-10% din veniturile anuale sunt cheltuite pentru combaterea căsătoriei și a consecințelor acesteia. Cu Six Sigma, Motorola a economisit 16 miliarde de dolari din 1986 până în 2001.
De atunci, metodologia a fost adoptată de mulți grei industriali și financiari. Producător de mașini Vad datorită Six Sigma, și-a crescut veniturile în 2000 cu 300 de milioane de dolari.Compania a cheltuit câteva milioane pentru pregătirea personalului în metodologie și nu a regretat. PM a creat o serie de proiecte de succes care i-au încântat pe clienții Ford.
General Electric Este una dintre primele companii care a folosit dezvoltarea Motorola. Directorul executiv Jack Welch a început pregătirea personalului în Six Sigma în 1995. Timp de 13 zile și 100 de ore, managerii au trecut printr-un program bogat. Green Belt a devenit o cerință pentru promovare, iar implementarea cu succes a metodologiei a crescut prima cu 40%. Managementul superior venea adesea la prelegeri pentru a răspunde personal la întrebările personalului.
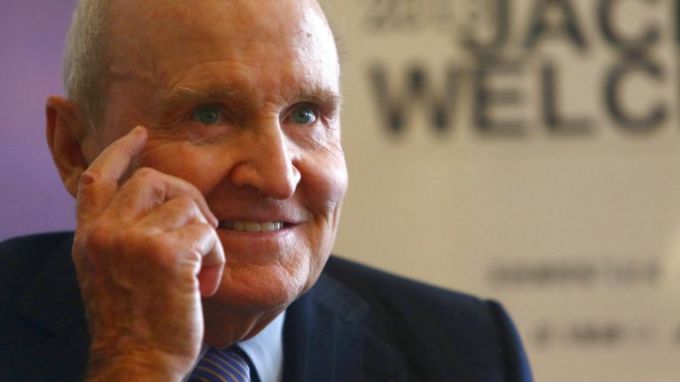
General Electric a investit nu doar în formarea propriilor angajați, ci și în companii de externalizare. Deja în 1997, profitul corporativ al GE a crescut cu 700 de milioane de dolari, iar în cei trei ani de program, compania a primit încă 4,4 miliarde de dolari.
A treia cea mai mare bancă din Statele Unite Banca Americii a folosit principiile Six Sigma în 2005 pentru a reduce timpul necesar pentru a deschide un cont de internet. Numărul de pași ai clienților a scăzut de la 10 la 4. A devenit mai ușor pentru utilizatori să se autentifice, acum au suport text online. Ca urmare, numărul creditelor și depozitelor a crescut brusc, iar banca și-a crescut profiturile cu 30%.
Producător de avioane Boeingîn 1999 a lansat o formare pe scară largă a personalului în principiile Six Sigma. Compania a produs aproximativ 60 de Centuri Negre și peste 300 de Centuri Verzi. Boeing a redus costurile cu 210 milioane de dolari în 5 ani.
În 2007, 82 dintre cele mai mari 100 de organizații din SUA implementau principiile Six Sigma. Mulți dintre ei au fost lideri în industria lor și la nivel internațional. Iată un studiu care a demonstrat că peste 4 ani de implementare, companiile au primit suplimentar 1-7% din profit.
Companii de TOP și profitul lor cu Six Sigma
Anul lansării Six sigma | Companie | Tip de afacere | Venituri în 2008, milioane de dolari | Cantitate muncitorii |
Fabricarea telefoanelor mobile | ||||
Constructii, management de proiect | ||||
automatizare si control | ||||
Echipament de productie | ||||
Industria chimica | ||||
Produse farmaceutice | Necunoscut |
|||
Sectorul bancar | ||||
Productie auto | ||||
General Electric | Fabricarea de utilaje |
Companii de top și economiile lor cu Six Sigma
Companie | Perioada observată | Venituri totale pentru perioada observată, milioane USD | Suma economisită, milioane de dolari | Suma economisită, % din venit |
General Electric | ||||
Cărți
Rezolvarea unor probleme industriale complexe fără statistică / Ralph Polak, 2016
Pentru acei adepți Six Sigma care nu sunt deosebit de puternici în partea matematică a metodologiei. În schimb, autorul oferă 14 exemple practice în care predă „gândirea de calitate”. Polak dezvăluie cum să distingem rapid între producția proastă și bună și cum să găsiți vizual „indicii” care vor duce la cauzele defectelor. Tratează analiza calității ca pe un sondaj la locul crimei, ne îndrumă autorul.
Calea Six Sigma. A Practical Guide for Implementation Teams / Pete S. Pandy, Robert P. Newman, Roland R. Caveneg, 2005
Compus de trei antrenori care lucrau pentru General Electric. Acesta explică cum să utilizați instrumentele și șabloanele Six Sigma pentru a aduna informații, a îmbunătăți productivitatea și a reduce costurile.
Lean Six Sigma / Michael L. George, 2007
Autorul și-a fondat propria companie de consultanță, în care a implementat managementul bazat pe ideile Six Sigma și Lean. George a descris cum să îmbunătățească calitatea produsului și să reducă timpul de lansare folosind două metodologii.
Six Sigma for Dummies / Craig Gigi, 2008
Tradițional pentru începători, în care bazele metodologiei sunt explicate într-un limbaj simplu.
Aplicații și programe
Saas-serviciu de management de proiect, care permite gestionați proiecte, sarcini și liste de verificare. Toate principiile vizualizării intuitive, diagrama Gantt și panourile Kanban sunt implementate aici (din octombrie 2017, este deja în testare beta).
Cu Worksection, este convenabil să urmăriți activitatea echipei și progresul întregului proiect. Utilizați instrumente Six Sigma:
- prescrie planuri de îmbunătățire a sarcinilor cu liste de verificare sau subsarcini
- marcați cei responsabili pentru upgrade-uri, monitorizați progresul și finalizarea în timp real
- analizează rezultatele în rapoarte, implementează tehnologii de succes
- stabiliți bugetul și cheltuielile pentru experimente chiar în sarcini.
Aplicație pentru iOS. Creați diagrame, măsurați performanța, utilizați instrumente statistice, personalizați accesul rapid la documente și aruncați o privire asupra definițiilor termenilor.
Un program pentru iOS care vizualizează fluxul de lucru. Creați carduri în care să atribuiți rolurile interpreților, precum și să lăsați comentarii și sugestii. Urmărirea convenabilă a execuției proceselor.
Cerere de pregătire pentru examene la ASQ. Conține 300 de întrebări pentru candidați în Centuri Negre și Centuri Verzi ... Sprijinit de Android și iOS.
Se integrează în Microsoft Excel. Conține instrumente statistice de bază Six Sigma.
Verdict
Six Sigma este o strategie care te învață cum să cauți defectele și cauzele lor în organizație.
Pentru aceasta se folosesc instrumente statistice, planificarea experimentelor și managementul continuu al calității. Succesul aplicației Six Sigma depinde de pregătirea managerilor de proiect și de interacțiunea acestora cu personalul.
După cum se calculează în Occident, un deținător de centură neagră bine antrenat este capabil să realizeze 5 sau 6 proiecte în 12 luni. Un astfel de specialist va economisi organizația cu 175 de mii de dolari și va adăuga 1 milion de dolari la profitul anual.
Ar putea fi util să citiți:
- Descrierea postului pentru director de management de proiect;
- Planul de producție în planul de afaceri: descriere, funcții, conținut;
- Rata internă de rentabilitate - IRR;
- Investiții de capital fix: tipuri și surse;
- Utilizarea unei hărți de risc pentru a le identifica;
- Automatizarea sistemului de management al proiectelor;
- Cum se face un proiect?;
- Raționalizarea forței de muncă: tipuri de norme și standarde;